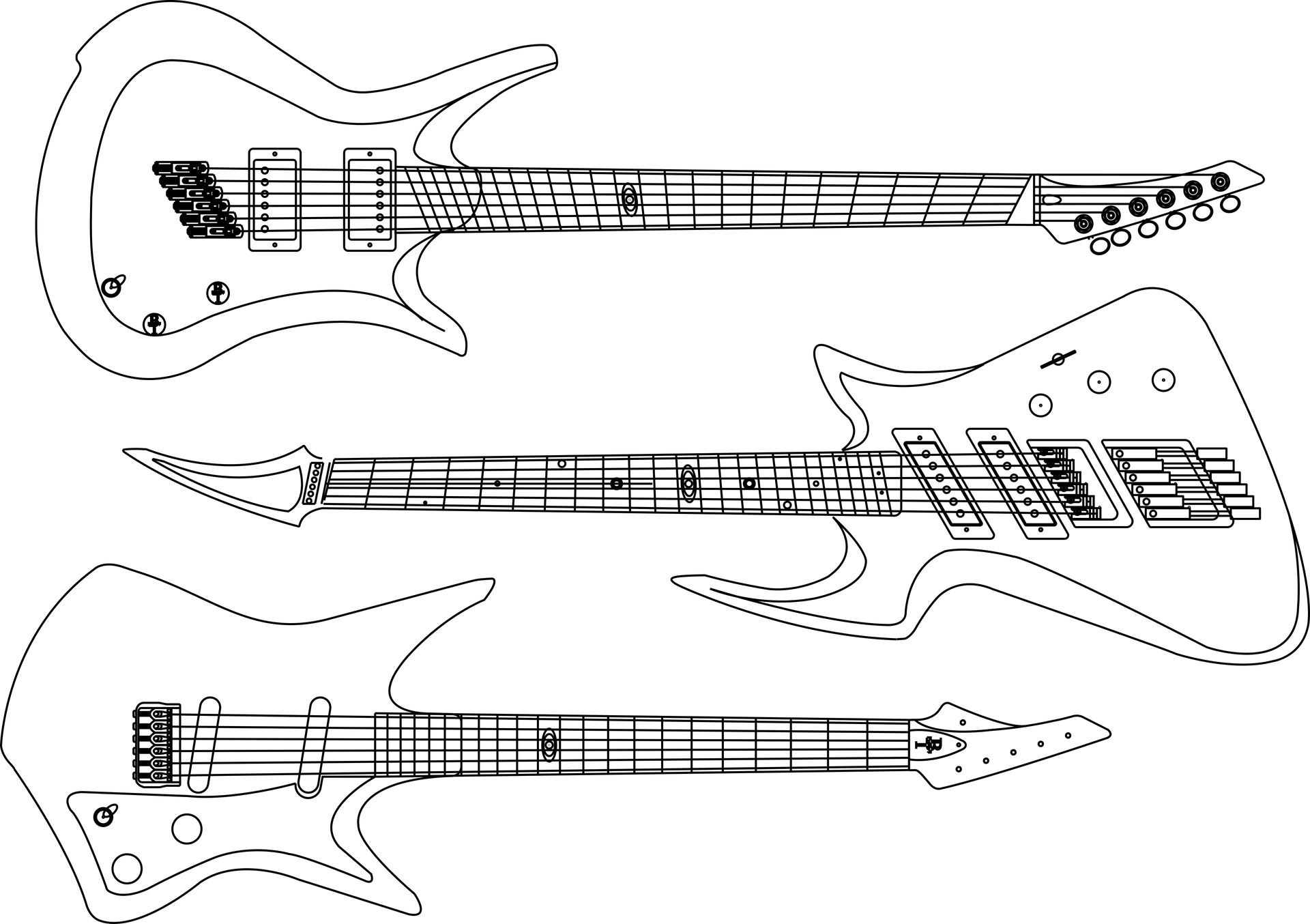
Why Gibson Headstocks Break
(In Progress)
An In-Depth Look at the Physics Behind One of the Most Common Guitar Injuries

The Demise of Many a Gibson Headstock
Unfortunately, a Gibson headstock breaking is about as common as someone playing Smoke on the Water or Stairway to Heaven. It happens all the time whether you like it or not. There are many explanations on the internet about why Gibson headstocks break, but many of them address only one facet of the underlying physics of Gibson headstock breakage. So today, we are going to look at the more complete picture.
Understanding Wood
​
The first thing we need to understand before we dive into what specifically makes the Gibson headstock prone to breakage is to understand the material that it is made from. Wood is a fantastic natural resource that has many incredible attributes. However, like all materials, it benefits from understanding its strengths and weaknesses.
​
When a tree grows, the primary source of lumber is the trunk (known as the bole in the lumber industry). This results in the largest, straightest boards with the least likelihood of knots, warping, etc. When we refer to the grain of the wood, we refer to the end grain and the long grain. If you were to take a log, the end grain is what shows on the ends (Amazing!) and the long grain is the grain that runs along the length of the log (Double Amazing!) Each of these grains is optimized for a strong and healthy tree.
​
The end grain can bear immense amounts of load, like the entire rest of the tree. It is strong and stiff. The long grain can resist shear (sideways) loads, like during the wind. In these situations, they are true wonders of nature. Try to subject them to loads that they are not used to, and they will quickly become compromised. This is due to how the tree fibers grow and are arranged. The long grain can be thought of as long strands of wood fiber, bound together with cellulose, that allows water and nutrients to go from the roots, up the trunk, and to the limbs. This arrangement, however, means that long grain can be separated relatively easily from long grain. This is the whole reason that you can chop a sizable piece of wood in two when strong the ax in the direction of the long grain; it naturally splits along that grain.
Basic Neck Construction and Force Diagram
​
Now that we understand the makeup of wood a little better, let's look at how we use this incredible material to construct a neck. The forces on a guitar neck are the tension of the strings and any flexion introduced by grabbing and holding it. So the ideal grain arrangement is to have the long grain run the length of the neck. The end grain with its high stiffness will resist the compression force of the string tension while the long grain will resist the flexing force of the strings as well as holding the neck, falling, etc. The force diagram below illustrates these forces.
Gibson-Specific Design Factors
​
With the basics of neck construction down, let's look at some design features of the Gibson neck/headstock that are of interest to our discussion. These are: grain runout, headstock angle, and truss rod route. Let's look at each of these a little more closely.
​
Grain Runout
​
The first feature of the Gibson headstock is that it has no scarf joint. This is not necessarily a problem, as Fender headstocks have no scarf joint either. It is the combination of no scarf joint and a non-zero headstock angle where the first signs of trouble are introduced. However, we are going to look at the grain runout.
​
So what do we mean by grain runout? Remember our long grain? Well, if you cut across the long grain at an angle, the termination of that grain on the angled surface is what is called runout. Runout can also mean any grain that deviates from straight, but we will use the slightly less correct definition here. Note in the diagram below how the headstock appears to "cut across" the grain. Because there is no scarf joint, the possibility exists for breakage along the grain line. This is where the headstock angle comes in to play.
Headstock Angle
​
The headstock angle coupled with having no scarf joint is the primary cause of Gibson headstock weakness. To add insult to injury, Gibson uses a very steep headstock angle, 17 degrees. Most modern headstocks use an angle of 10-14 degrees, with some brands like Rickenbacker going as low as 5 degrees. Even Fender manages with no angle, but they do have those string trees, for better or worse. In the image below, notice how the amount of grain runout on a 17 degree headstock compares to that of a 10 degree headstock. The difference is quite noticeable.
Truss Rod Route
​
The third feature of a Gibson headstock that we want to consider is the truss rod route. Old-style truss rods are a piece of steel threaded one direction and were used purely for correcting the neck bending forward under the strain of the strings. Guitar makers in the early days each came up with their own method of making them, ranging from the non-adjustable square metal tubes of Martins to what Gibson ended up with, which is a threaded rod with a brass nut and a washer at the headstock end. This accomplishes the goal of having a functional truss rod, but at a cost. The truss rod route removes a lot of material right where it is weakest. All that material had to be removed in order to fit the half-moon washer in there and leave enough room for a truss rod wrench to adjust turn the nut.
Strength Comparison
​
The above is what most treatments of the topic will deal with. However, let's take a look at how those factors combine when compared to a slightly more modern neck and headstock design. For the sake of this comparison, we will assume identical neck material, neck and headstock thickness, and both necks will not have a scarf joint. To get started, let's recall our long grain strength in our wood. The strength of the material is proportional to the amount of area, or contact surface, between wood fibers. This will take into account the length of the grain running through the headstock area as well as the effective width.
​
Grain Runout and Headstock Angle
​
If we use a nominal headstock thickness of .625" (5/8"), then the 17 degree headstock results (using a 1/sin(x) relationship) in a long grain length through the headstock of 2.XX". Now, if we consider a more modern neck angle of 10 degrees, that long grain length becomes 3.YY". This means that the Gibson headstock has a long grain length of only 54.1% of that of a more modern headstock design. So right off the bat, the Gibson headstock has only 54% the strength of a modern headstock angle.
​
Truss Rod Route
​
The headstock angle isn't the only contributing factor, however. The truss rod route width for a traditional Gibson is 9/16". Modern two-way truss rods typically require a route of no more than 3/8". For a neck with a nut width of 1 11/16" (pretty standard), this results in the Gibson headstock having only approximately 88% the amount of effective headstock width. This combines with the long grain length to give us relative contact areas for the wood fibers. This results in 0.88*0.54 = .475. This means that the Gibson headstock with its 17 degree angle and truss rod route is only about 47.5% as strong as a headstock with more modern parameters. That means a break is more than twice as likely.
​
Headstock Angle, Revisited
​
But wait, there's more! In addition to the Gibson headstock angle resulting in less long grain length, the headstock angle results in an increased lever arm. Not sure what a lever arm is? Well, it's what causes a force to exert torque on a pivot point. So what does that mean? Well, the pivot point of the headstock is the point at which the angle begins. If the guitar falls and the headstock hits, the force of impact exerts a torque on the pivot point. The lever arm is proportional to the sine of the headstock angle, which means that a larger headstock angle will be able to exert more force on impact on the weakest portion of the headstock. If we compare the sin(10*) and sin(17*), we note that the steeper angle results in 1.04 times (4%) more torque exerted. This may not seem like a lot, but when taken into account with the contact area for the wood grain, we have a total strength of about 45.7% for a Gibson compared to a headstock with a 10 degree angle and a smaller truss rod route.
Different Construction Techniques
​
All the above assumed two headstocks made without lamination or scarf joints. Both lamination and scarf jointing greatly increase headstock strength due to wood glue bonding together grain that runs in differing directions. This action of grain running in different directions can increase the strength of the joint many fold. This means that a modern headstock that is constructed with a scarf joint and/or lamination can be up to 10 times or more stronger than a Gibson headstock. This is why Gibson headstock breaks are far and away the most common ones seen. That doesn't mean others don't exist, it simply means they are much less common.
​
So there you have it, a breakdown not only of why Gibson headstocks break, but an analysis of just how much weaker they are compared to headstocks with only modest changes to the design.